The aircraft, ships, and lorries of the future must be powered by e-fuels—fuels produced partly from captured CO2—and partly from hydrogen produced by the splitting of water.
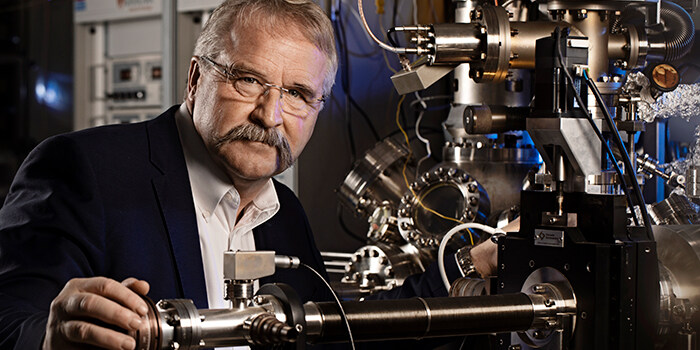
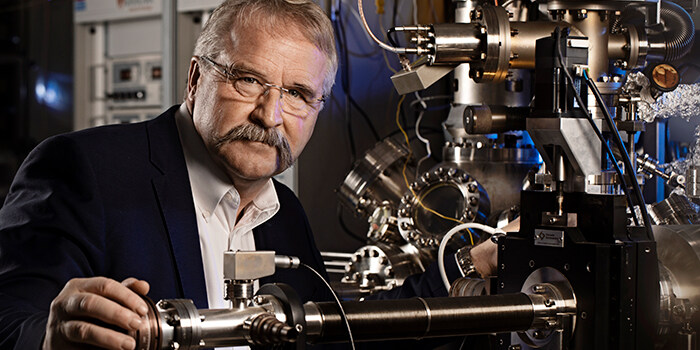
“Of course we can get Greta Thunberg to take to the skies!” There is no hesitation from Ib Chorkendorff, professor at DTU Physics and Head of The VILLUM Center for the Science of Sustainable Fuels and Chemicals.
“In principle, we’re already able to power aircraft, ships, and cars without carbon emissions—the only question is which of the possible technologies will be the most effective. Ultimately, it all comes down to economics.”
According to the physics professor’s vision, aircraft, ships, and lorries of the future will be powered by so-called electro-fuels—also called e-fuels—which are short for the English word electrofuels. E-fuels can potentially replace fossil fuels in heavy-duty vehicles that are difficult to electrify.
E-fuels can be produced using electrolysis. Electrolysis is the chemical splitting of substances in a solution using an electrical current. Thus, it is possible to split water into its two components—hydrogen and oxygen. When you then allow the hydrogen to react with CO2 you can make methanol, which is a liquid fuel.
Eco-friendly fuel
Electrolysis requires energy in the form of electricity. If we ensure that this electricity comes from renewable energy sources such as wind turbines and solar cells, we can produce hydrogen with zero climate impact. Aircraft, ships, and lorries of the future must be powered by e-fuels—fuels produced partly from captured CO2 and partly from hydrogen produced by splitting water. CO2 can also be captured by burning biomass.
“This way we can let Greta Thunberg airborne on eco-friendly fuel. But one of the points is that we shouldn’t pump CO2 underground—a solution many people have shown an interest in. Yes, we need to capture CO2, but it has to be a valuable raw material for the production of e-fuels,” says Ib Chorkendorff.
The oxygen produced during the electrolysis process can also be exploited—namely, as an excipient.
“On the one hand, pure oxygen provides superior combustion when biomass is incinerated to provide electricity, heat, and CO2—and on the other hand, pure oxygen makes it much easier to extract CO2, as it has not been diluted with the nitrogen from the air,” explains Ib Chorkendorff.
German tanks powered by Power-to-X
One name for many technologies. The concept that Ib Chorkendorff and his colleagues are working on is also called ‘Power-to-X’. The term covers a number of technologies that start with the production of hydrogen by means of electrolysis—i.e. using electricity—‘Power’, which is then used to produce liquid fuels, chemicals, gas—or something completely different. In other words ‘X’.
Ib Chorkendorff says we should not be fooled by the technical sounding name: “Power-to-X isn’t rocket science. As early as World War II, the Germans produced fuel from coal when they had trouble maintaining oil supplies. They used the so-called Fischer-Tropsch method whereby coal and water are first converted into a mixture of CO and hydrogen, which is subsequently converted into liquid hydrocarbons with the help of a catalyst. The method is hardly economically viable, but the German army desperately needed fuel. Towards the end of the war, the entire German army ran on fuel produced using the Fischer-Tropsch approach.”
Hydrocarbons are interesting, as they are found in large quantities in fossil resources. But they can also be manufactured.
“If you can get hydrogen from electrolysis and CO2 from burning biomass in pure oxygen, you can, in principle, build up your hydrocarbons in a sustainable way,” says Ib Chorkendorff, who takes his vision a step further: “In the long run, one could imagine these processes being interconnected. Instead of producing hydrogen, the electrolysis could connect its protons directly to CO2, thereby building up hydrocarbons. This is a very hot area of research where researchers are trying to do things in a novel way—no more novel, however, than what nature already does through photosynthesis!”
Price of electricity a barrier
The above methods involve high energy consumption, negatively affecting the climate accounts for Power- to-X—but that situation will change, assures Ib Chorkendorff: “After all, the energy to power the processes comes from electricity. Here, I think we can afford to look beyond the current situation where our energy production generates CO2 emissions. In the near future, where wind turbines and solar cells produce copious amounts of climate neutral power, this will no longer be a problem. With regard to the need for CO2 as a raw material, we’re talking about recycling, as we get CO2 from incinerating biomass. As plants grow, they take carbon dioxide from the atmosphere. Overall, the process is therefore completely CO2 neutral.”
However, he acknowledges that climate impact is only part of the problem associated with high energy consumption. It will also be about money: “For me, the question is not whether we can create climate-neutral fuels, but how much we are willing to pay for them. If we imagine that fossil fuels were two and a half times as expensive as today, then e-fuels would start to become relevant. However, the technology needs to be significantly improved. The challenge is to make the technology so cheap and efficient that it can compete with fossil fuels.”
Up against 100 years of fossil solutions
A key phrase going forward is the ‘development of new catalysts’. The current production of gasoline, solvents, plastics, and a wide range of other petroleum products is based on catalytic processes developed over the last 100 years and which have undergone continual refinement. On the other hand, the manufacture of e-fuels and a number of other products with low climate impact and high sustainability has only just begun, and there is a need to develop completely new processes and catalysts for this purpose.
Just outside Ib Chorkendorff’s office is a staircase leading down to the experimental hall where the development of catalysts is in full swing. These are catalysts for the production of hydrogen, liquid fuels, chemicals, and a wide range of other products. Many of the research group’s projects are carried out in collaboration with Haldor Topsøe A/S—a world-leading manufacturer of industrial catalysts.
“The cooperation with Topsøe is of great value to us. It’s important to have the industry on board, as it increases the chances of our ideas being realized. To begin with, Topsøe has extensive upscaling expertise.”