Advances in 3D concrete printing technologies are creating exciting opportunities to build homes faster, more sustainably and at reduced cost. University of Canterbury (UC), architectural engineer Dr Giuseppe Loporcaro is leading a research project to refine low-carbon, seismically resilient solutions for 3D printed homes suited to New Zealand conditions.
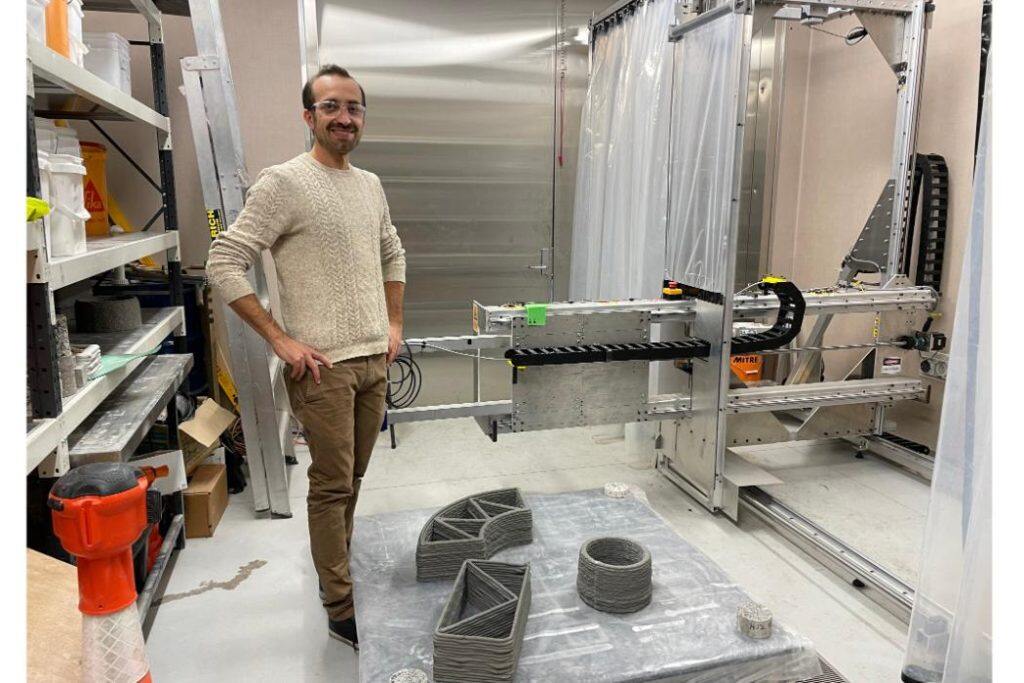
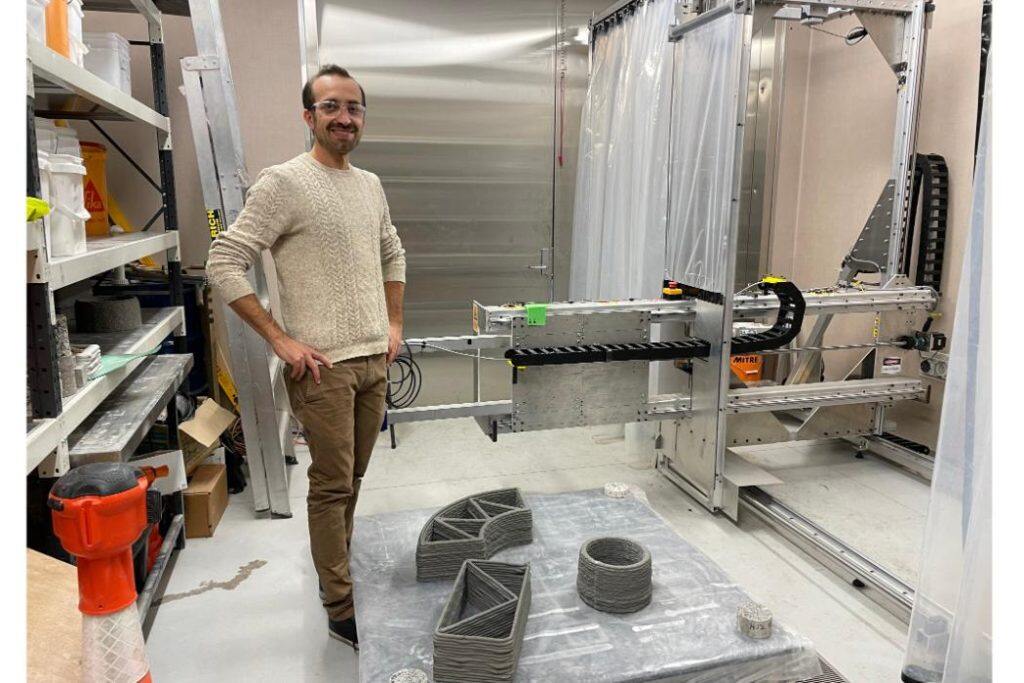
Research in this field has been gaining momentum at UC over recent years. In the Department of Civil and Natural Resources Engineering, a machine has been built to 3D print concrete walls by extrusion and students at both undergraduate and postgraduate level have been exploring materials for the process.
Over the next three years, Dr Loporcaro and his team plan to further extend their knowledge and expertise as they seek to unlock the potential of this alternative construction technology. The first phase will involve further refinement of materials used for 3D concrete printing.
“Low carbon is an important aspect of our research,” says Dr Loporcaro. “We plan to build on our research to date, developing sustainable material for 3D concrete printing, for example, re-using mussel shell waste and other resources. We also plan to optimise the shape of elements so as to reduce the total amount of material needed along with carbon dioxide emissions.”
The project’s second phase will focus on design and structural engineering. “We will really be focusing on what a 3D printed house would look like in Aotearoa New Zealand and considering how to make something suitable for our communities, rather than repeating what has been done overseas.”
Creating seismic resilience by integrating high strength steel into 3D concrete printed walls – possibly alongside natural fibres or other reinforcements – is a key research goal.
Callaghan Innovation will be sharing their expertise on concrete in this project, providing advice and feedback as the research proceeds.
“We are also actively partnering with a 3D concrete printing company in New Zealand called QOROX. They will be part of our technical advisory team and the partnership will also allow us to print larger scale 3D printed elements.”
With demand for housing in New Zealand outstripping supply – made worse by a global pandemic and associated supply chain disruption – there is clearly a place for alternative construction technology that brings greater automation to the sector. New low carbon approaches are also needed if Aotearoa New Zealand is to achieve zero carbon by 2050.
“Affordability is another big issue in our housing market; 3D concrete printed homes would offer a cheaper alternative and would help bring down the costs of construction.”
This UC-led research, which also aims to finetune specifications for materials and structural design, is on track to bring commercial 3D concrete printed housing one step closer to full commercial reality.